Data analysis for the process industry
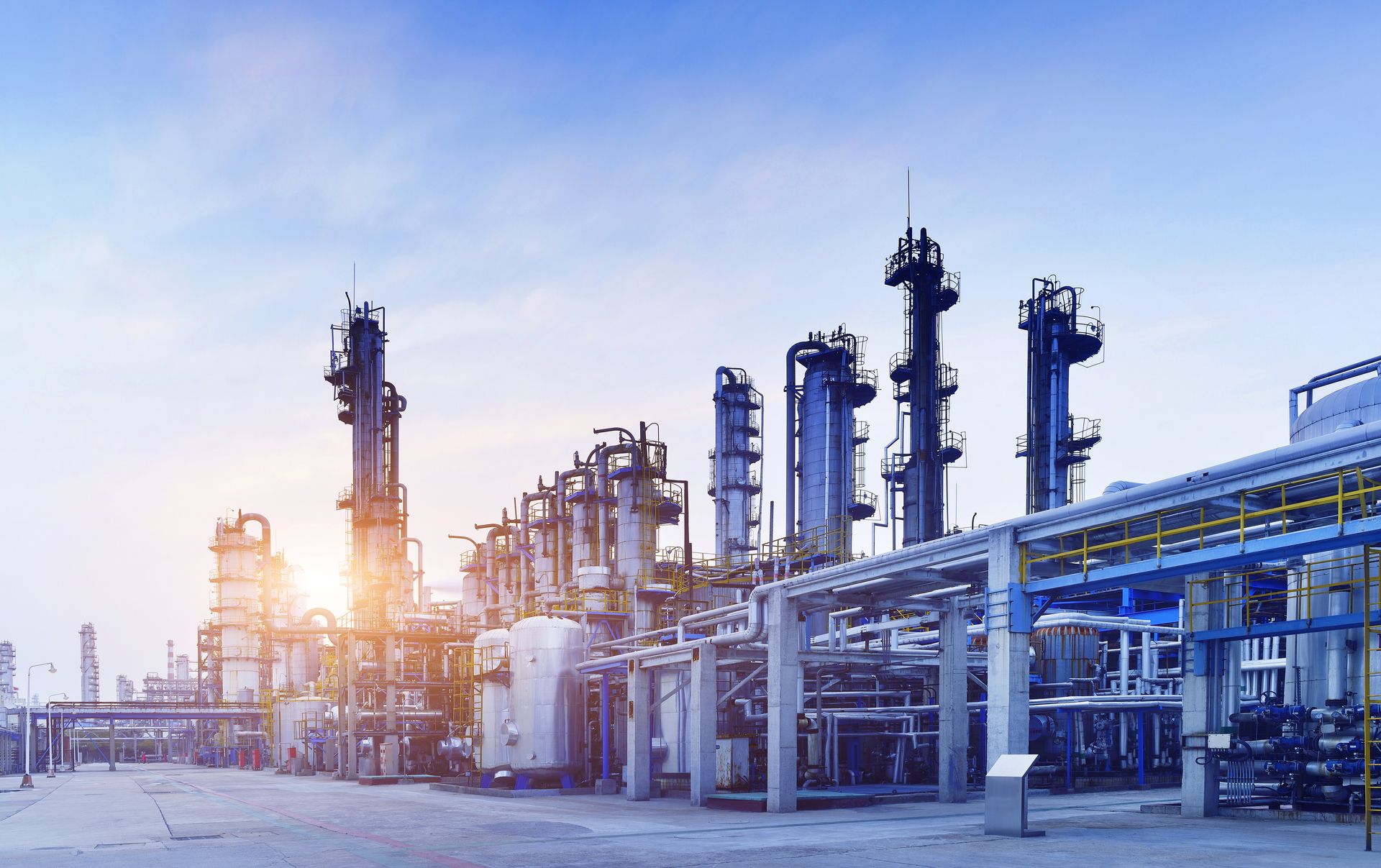
The largest mineral oil company in Central Europe uses TGUs (Thermal Gasoil Units) to treat crude oil and by-products/residues from other processes for further processing. KBC helped the company to aggregate and analyze existing data, develop process models based on it and thus find optimal operating modes for the coking process.
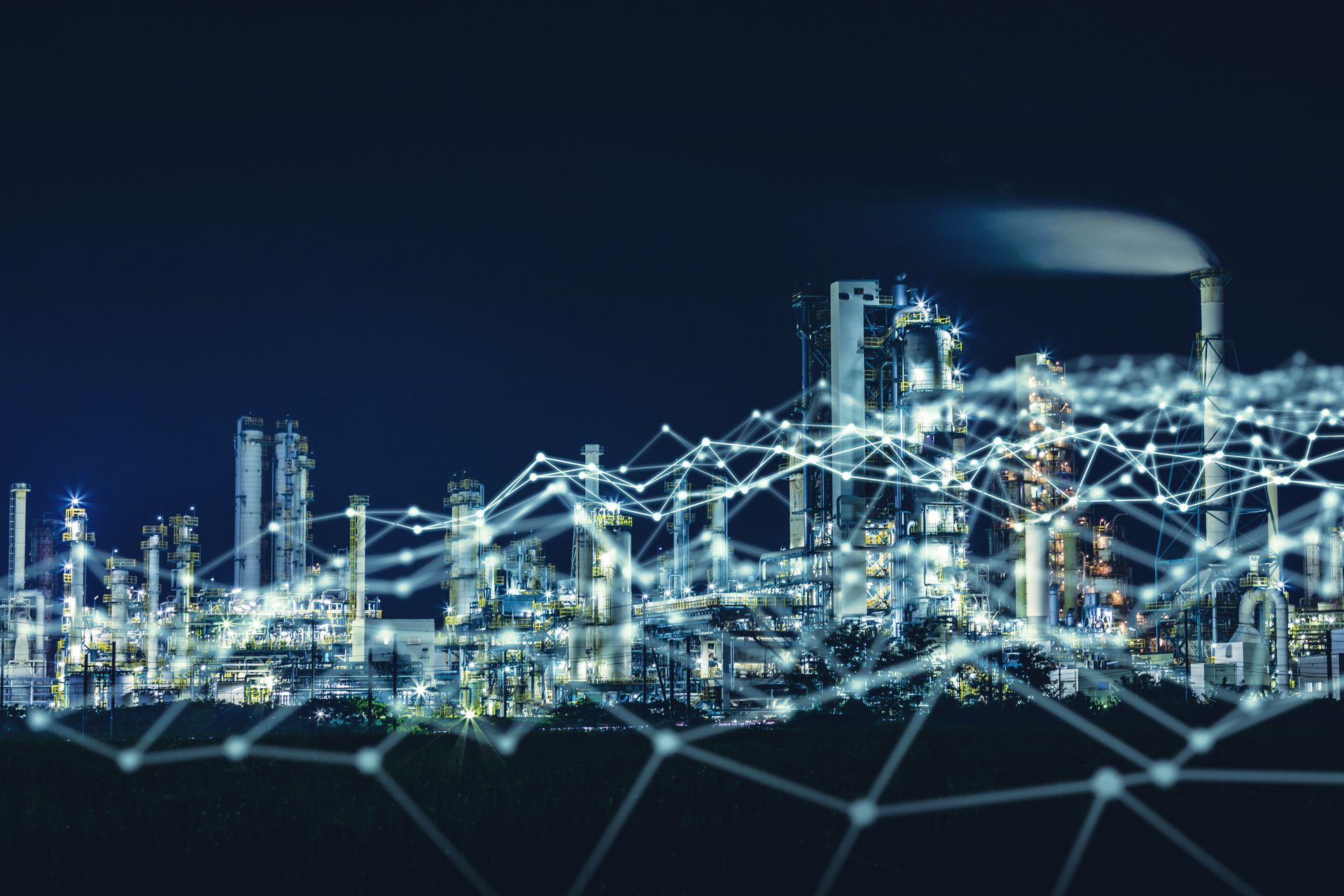
CANCOM Austria emerged from K-Businesscom (formerly Kapsch BusinessCom) at the beginning of 2024. The following case study was written before that and therefore the text was left in the original version.
Business Challenge
The company needed support in optimizing a thermal cracking process. Irregularities in the process and in the composition of the material supplied were causing coking in the combustion chamber. The company was therefore looking for a solution to dynamically determine the right parameters for stable conditions in the combustion chamber. Together with KBC, a software was to be developed that could predict the coking rate as accurately as possible and thus enable optimum combustion.
Solution
In the final expansion stage, the system makes it possible to find two operating modes that optimize either the thermal conversion performance of the process (best possible combustion) or the maintenance intervals (lowest possible coking residues). All running on Microsoft Azure.
Data analysis
- Data aggregation from laboratory data of the source material, sensor data and reports
- Data analysis and visualization in a dashboard
Sensors
- definition & calculation of "soft sensors"
- Classification model for source material
Software
- Modeling of the coking process in the combustion chamber
- Recommendation engine for process parameter settings