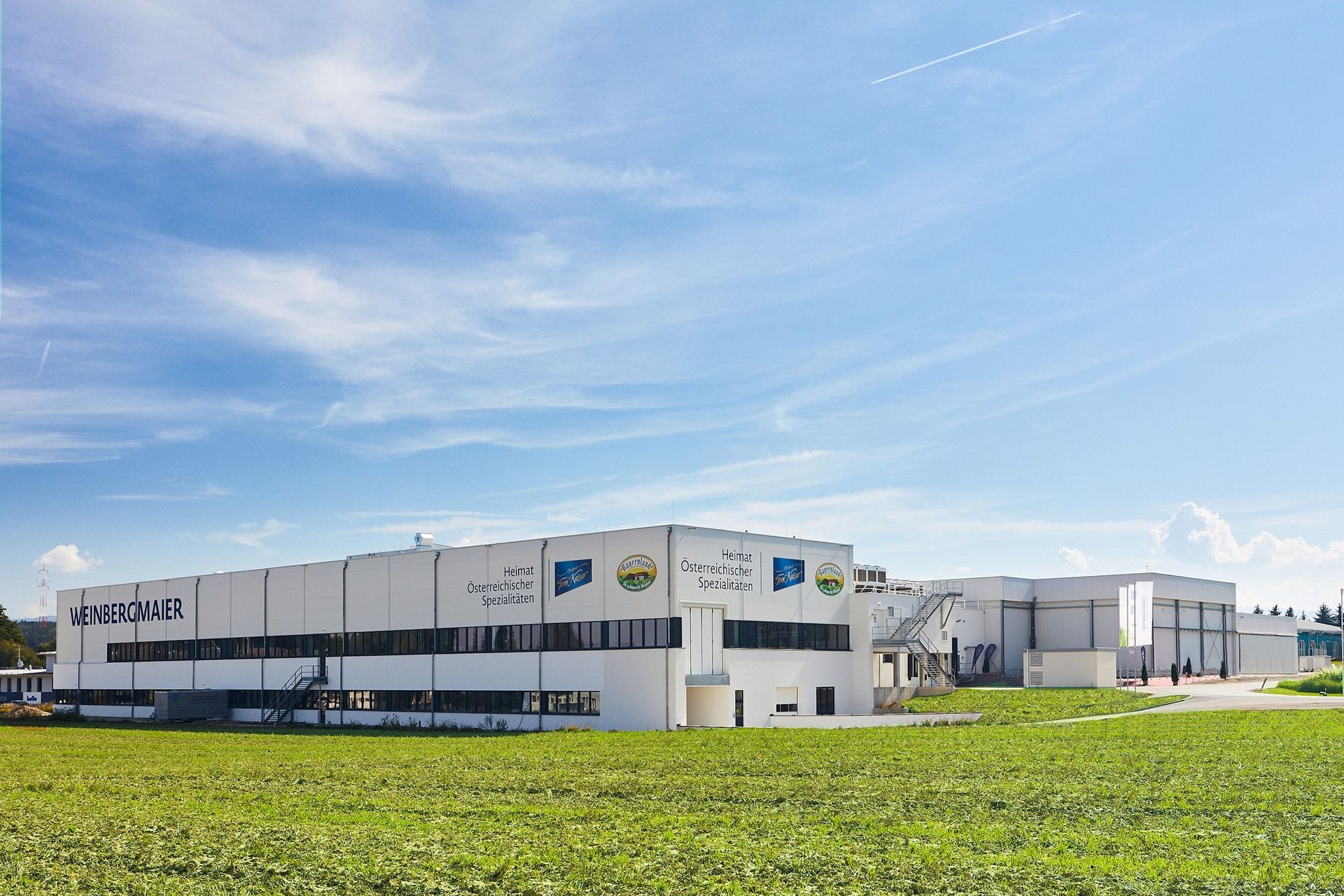
Strudel, dumplings or Kaiserschmarrn: WEINBERGMAIER'S digital master plan
"We are in a spirit of optimism," says Harald Fürlinger, Head of IT and Digitalization at WEINBERGMAIER. "In order to achieve our 2028 sales target, we are continuing to invest heavily in state-of-the-art, efficient production. At the same time, we are hiring new employees. To support the ongoing change process, we are now focusing on an overarching overall concept for digitalization."
From isolated solutions to a holistic, digital roadmap
The company commissioned the IT and digitalization experts at K-Businesscom (KBC) to develop such a concept. The professionals not only have certified technological expertise, but also special know-how in the food industry. The first step was for the digitalization experts to get a picture of the status quo: Which digital island solutions already exist? What will be needed in the future? Stakeholders from various areas of WEINBERGMAIER and KBC then came together in joint workshops. "Transparency with employees is important from the outset to ensure full commitment within the company," says Saskya Lipp, Business Consultant Manufacturing for the DACH region at K-Businesscom. "It is also important to demonstrate the benefits of digitalization solutions and to tailor the digitalization strategy precisely to the company. We attach great importance to tailoring the approach to the current task." This was also the case for WEINBERGMAIER: first, the teams collected creative starting points for the digital transformation from the ranks of the employees. This resulted in specific use cases, which were then assigned to the focus areas of the digitalization strategy. Using this approach, the team identified the most important milestones of the digital transformation. One of these milestones is the "automation of production lines". This consists of many individual measures, such as predictive maintenance, production data acquisition and packaging automation with the help of robotics.
Digitalization promotes employee satisfaction
Digitalization has already arrived in many areas and is leading to a noticeable reduction in tedious, repetitive and demotivating tasks. At the Vienna site, for example, "Franz and Sissi", two digitally networked robots, pack the strudel, while a software robot has taken over smaller tasks in the administration department. The aim is always to enable employees to devote themselves to tasks that require their expertise, thereby increasing employee satisfaction.
Digital customer exchange with a big impact
Another focus area is "networked communication". This focus area is divided into external communication with customers and suppliers, while internal communication concentrates on the company's employees. This enables efficient, automated processes to be implemented across company boundaries. "Despite the ongoing digitalization and automation, we still want to retain the flexibility to respond to individual customer needs," says Fürlinger. The switch to the new tools makes it easy to take individual customer wishes into account. "One of our customers preferred a fax order because of the transmission confirmation," says Fürlinger. "We have set up a digital assistant for this, which now searches through the incoming e-mail orders and sends an individual confirmation of receipt specifically for this customer."
"Digital roadmap" timetable
The planned projects are incorporated into the corporate strategy process and are subject to regular monitoring. "Today, the digital roadmap gives us transparency about the current implementation status of projects at all times and enables effective planning," says Fürlinger. "The view of the experts from the outside has helped a lot to move the process forward."
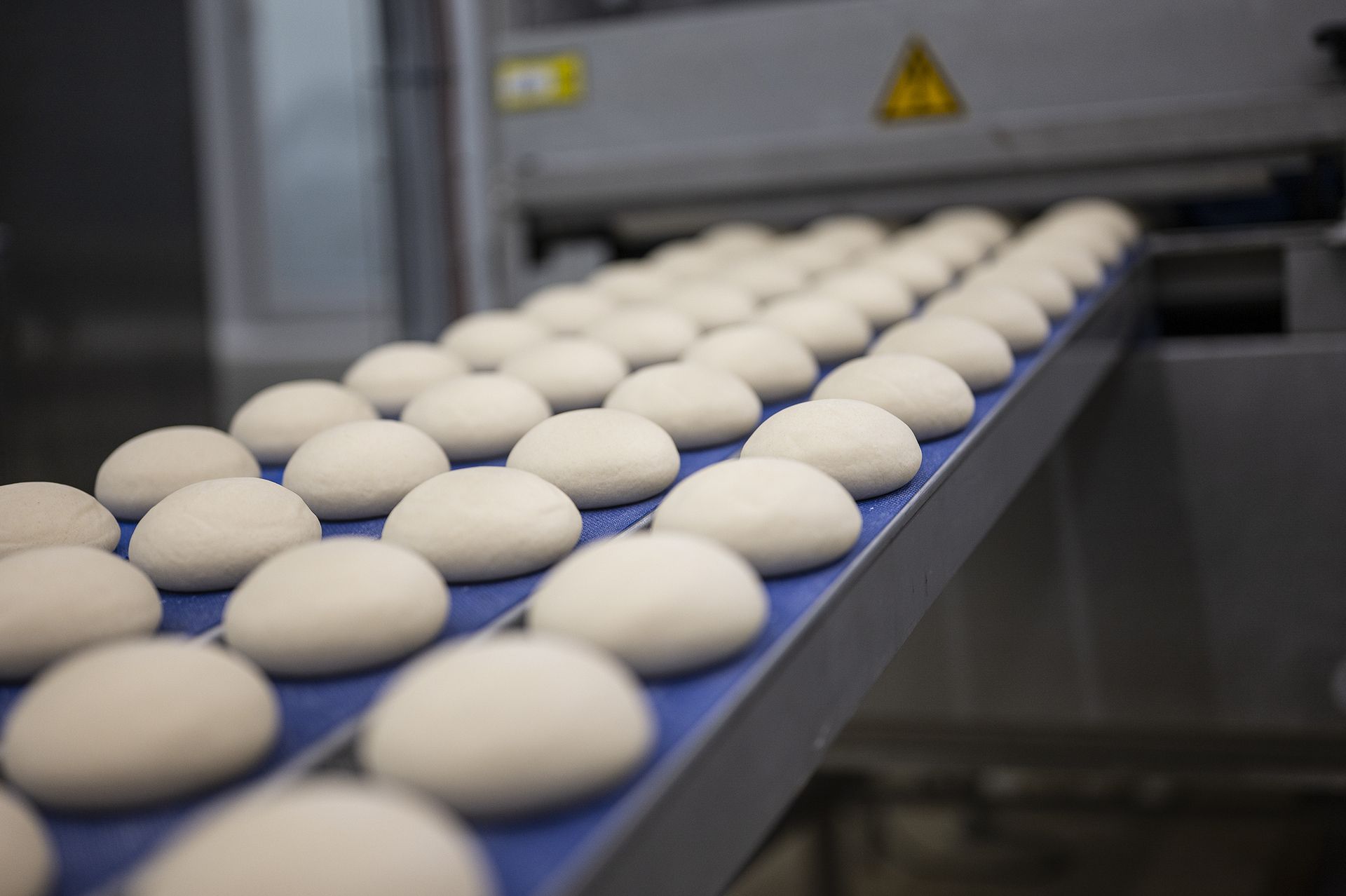